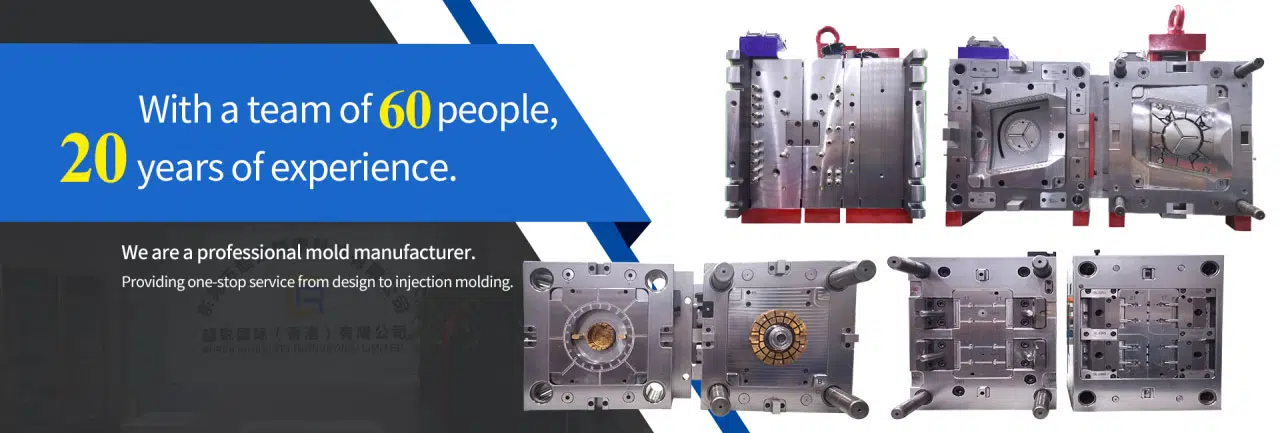
# High-Precision Machining Technology and Applications
## Introduction to High-Precision Machining
High-precision machining represents the pinnacle of manufacturing technology, where components are produced with extremely tight tolerances and exceptional surface finishes. This advanced manufacturing approach has become indispensable in industries where even micron-level deviations can significantly impact product performance.
## Key Technologies in High-Precision Machining
### 1. CNC Machining Centers
Modern CNC (Computer Numerical Control) machining centers form the backbone of high-precision manufacturing. These sophisticated machines offer:
– Sub-micron positioning accuracy
– Advanced thermal compensation systems
– Vibration damping technologies
– Multi-axis capabilities for complex geometries
### 2. Ultra-Precision Grinding
When surface finishes below Ra 0.1 μm are required, ultra-precision grinding becomes essential. This process utilizes:
– Diamond or CBN (Cubic Boron Nitride) wheels
– Precision spindles with nanometer-level runout
– Advanced coolant delivery systems
Keyword: High-Precision Machining
– In-process measurement capabilities
### 3. Micro-Machining Technologies
For components measured in micrometers, specialized micro-machining techniques are employed:
– Micro-EDM (Electrical Discharge Machining)
– Laser micromachining
– Ultrasonic-assisted machining
– Ion beam machining
## Applications of High-Precision Machining
### Aerospace Components
The aerospace industry relies heavily on high-precision machining for:
– Turbine blades with complex cooling channels
– Fuel system components
– Guidance system parts
– Structural components with tight weight tolerances
### Medical Devices
Precision machining enables life-saving medical technologies:
– Orthopedic implants with porous surfaces for bone integration
– Microscopic surgical instruments
– Dental prosthetics with perfect fit
– Implantable electronic devices
### Optics and Photonics
The optics industry demands exceptional precision for:
– Telescope mirrors and lenses
– Laser system components
– Fiber optic connectors
– Camera lens elements
## Future Trends in High-Precision Machining
The field continues to evolve with several emerging trends:
– Integration of AI for real-time process optimization
– Hybrid manufacturing combining additive and subtractive processes
– Nanometer-level machining capabilities
– Sustainable precision machining with reduced waste
– Increased automation for 24/7 production
As technology advances, high-precision machining will continue to push the boundaries of what’s possible in manufacturing, enabling new innovations across multiple industries.
No responses yet