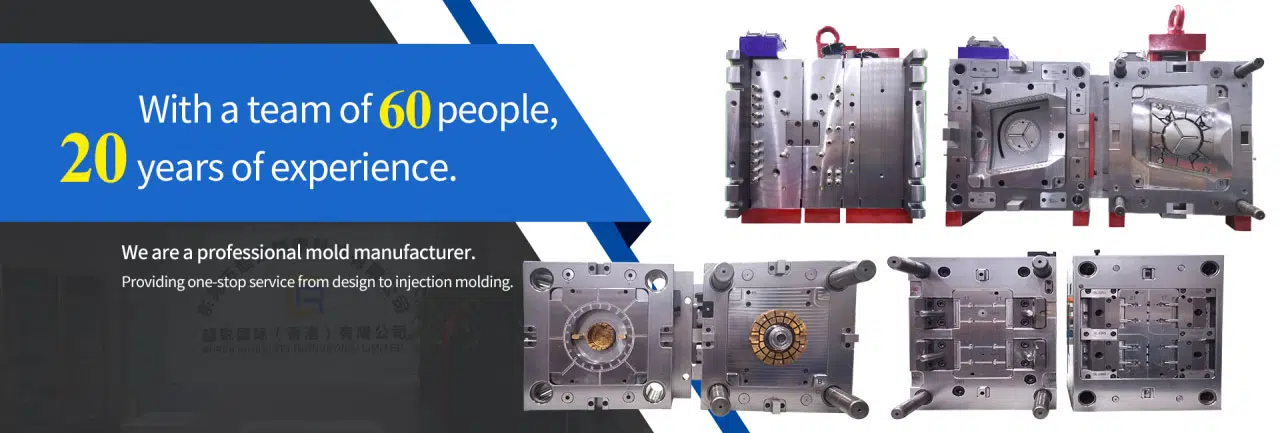
# Precision Engineering: Mastering Tight Tolerances in Manufacturing
## The Importance of Tight Tolerances in Modern Manufacturing
In today’s highly competitive manufacturing landscape, achieving tight tolerances has become a critical factor for success. Tight tolerances refer to the permissible limit of variation in a physical dimension, ensuring that parts fit together perfectly and function as intended. As industries demand higher precision and reliability, manufacturers must continuously refine their processes to meet these exacting standards.
## Understanding Tolerance Standards
Tolerances are typically expressed in thousandths of an inch (0.001″) or hundredths of a millimeter (0.01 mm). The specific tolerance required depends on the application:
– Standard tolerances: ±0.005″ (0.127 mm)
– Precision tolerances: ±0.001″ (0.0254 mm)
– Ultra-precision tolerances: ±0.0001″ (0.00254 mm)
## Key Factors Affecting Tolerance Achievement
Several critical elements influence a manufacturer’s ability to maintain tight tolerances:
### 1. Machine Tool Capability
Modern CNC machines with high rigidity, thermal stability, and advanced control systems can consistently achieve tolerances within 0.0005″ (0.0127 mm). The machine’s repeatability and positioning accuracy are crucial factors.
### 2. Material Selection and Behavior
Different materials respond differently to machining processes. Factors like thermal expansion, work hardening, and chip formation must be considered when planning for tight tolerances.
### 3. Cutting Tools and Tool Wear
Precision-ground cutting tools with specialized coatings maintain their edge longer, reducing dimensional variation caused by tool wear during production runs.
### 4. Environmental Controls
Temperature fluctuations, vibrations, and even air quality can affect dimensional accuracy. Climate-controlled environments and vibration-dampening foundations help maintain consistency.
## Advanced Techniques for Tight Tolerance Manufacturing
Manufacturers employ various specialized methods to achieve exceptional precision:
### 1. Statistical Process Control (SPC)
SPC monitors production processes using statistical methods to detect and correct variations before they exceed tolerance limits.
### 2. In-Process Measurement
Advanced metrology equipment integrated into production lines provides real-time feedback, allowing for immediate adjustments.
### 3. Temperature Compensation
For ultra-precision work, machines may include thermal compensation systems that adjust for minute temperature changes affecting material dimensions.
### 4. Single-Source Machining
Completing all critical operations in one setup minimizes errors from multiple fixturing and handling.
## Industry Applications Requiring Tight Tolerances
Several sectors demand exceptionally precise components:
– Aerospace: Turbine blades and fuel system components
– Medical: Implants and surgical instruments
– Automotive: Fuel injection systems and transmission components
– Electronics: Semiconductor manufacturing equipment
– Defense: Guidance systems and weapon components
## The Future of Tight Tolerance Manufacturing
Keyword: Tight Tolerances
As technology advances, manufacturers are pushing the boundaries of what’s possible:
– Nanometer-level precision becoming more common
– Adaptive machining systems that self-correct during operation
– Advanced materials requiring new machining approaches
– AI-driven quality control systems predicting potential tolerance issues
Mastering tight tolerances requires a combination of advanced equipment, skilled operators, rigorous processes, and continuous improvement. As manufacturing evolves, those who can consistently deliver precision components will maintain a competitive edge in an increasingly demanding marketplace.
No responses yet