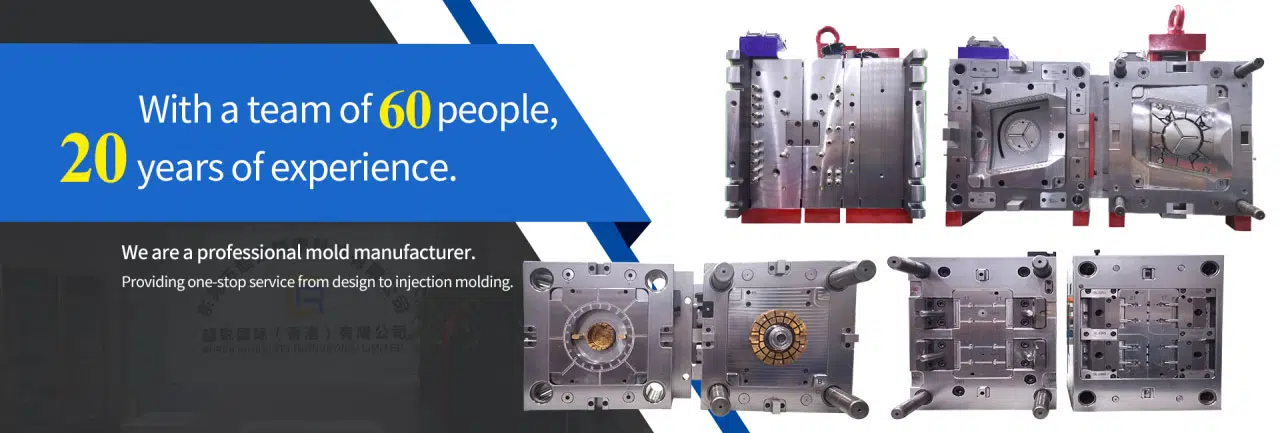
# High-Precision Machining: Techniques and Applications in Modern Manufacturing
## Introduction to High-Precision Machining
High-precision machining refers to the process of manufacturing parts with extremely tight tolerances and exceptional surface finishes. This advanced manufacturing technique has become increasingly important in industries where component accuracy is critical to performance and reliability.
Keyword: High-Precision Machining
## Key Techniques in High-Precision Machining
### 1. CNC Machining
Computer Numerical Control (CNC) machining has revolutionized precision manufacturing. Modern CNC machines can achieve tolerances as tight as ±0.0001 inches (0.00254 mm) through:
– Advanced servo motor control
– High-resolution linear scales
– Temperature compensation systems
– Vibration damping technologies
### 2. Micro-Machining
Micro-machining techniques enable the production of extremely small components with features measured in micrometers. Common methods include:
– Micro-milling
– Micro-turning
– Micro-EDM (Electrical Discharge Machining)
– Laser micro-machining
### 3. Ultra-Precision Grinding
This process uses specialized grinding wheels with micron-sized abrasive particles to achieve:
– Surface finishes below 10 nm Ra
– Form accuracies within 0.1 μm
– Sub-micron dimensional tolerances
## Applications of High-Precision Machining
### Aerospace Components
The aerospace industry relies heavily on high-precision machining for:
– Turbine blades with complex cooling channels
– Fuel system components
– Landing gear parts
– Avionics housings
### Medical Devices
Precision machining enables the production of:
– Orthopedic implants with porous surfaces for bone integration
– Microscopic surgical instruments
– Dental components
– Implantable drug delivery systems
### Optical Components
High-precision techniques are essential for manufacturing:
– Telescope mirrors
– Camera lens elements
– Laser optics
– Fiber optic connectors
## Challenges in High-Precision Machining
Despite its advantages, high-precision machining presents several challenges:
– Thermal deformation of workpieces and tools
– Tool wear at microscopic scales
– Vibration control at high spindle speeds
– Measurement and verification of ultra-tight tolerances
– High equipment and maintenance costs
## Future Trends in Precision Manufacturing
The field of high-precision machining continues to evolve with:
– Integration of artificial intelligence for process optimization
– Development of new ultra-hard tool materials
– Advances in in-process metrology systems
– Hybrid manufacturing combining additive and subtractive processes
– Increased automation for 24/7 production
As manufacturing demands continue to push the boundaries of precision, high-precision machining techniques will play an increasingly vital role in producing the advanced components needed for modern technology.
No responses yet